As part of the complete package, Tech-Max uses a variety of non destructive testing procedures (both in-house and outsourced) to ensure that the materials used to make your parts meet your quality expectations. These non destructive examinations verify the material’s surface and internal integrity. When combined with our stringent dimensional tolerance inspections, these examinations round off a complete inspection package that ensure quality parts across different disciplines.
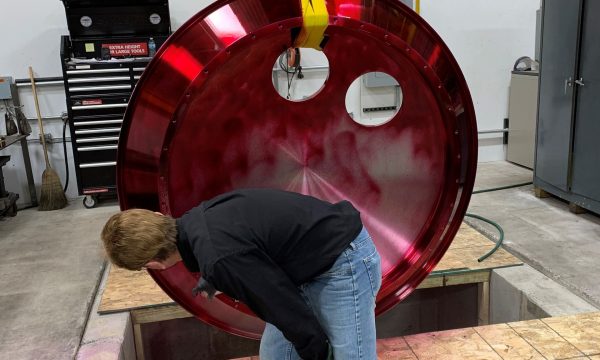